
OUR AMMONIA WILL REDUCE THE GREEN FUEL PREMIUM FOR SHIPPING LINES AND ENERGY GENERATORS AND CONSEQUENTLY THE CONSUMER
We enable green ammonia
Liquium has a new series of catalysts with more favourable operating conditons for green ammonia production whilst applying the well established and proven engineering Haber-Bosch process. This allows Liquium to scale and validate the technology quickly.
Liquium’s technology will help to significantly lower the capital and operating costs of all existing ammonia plants and new builds to help the uptake and delivery of the next clean liquid fuel for heavy industry.
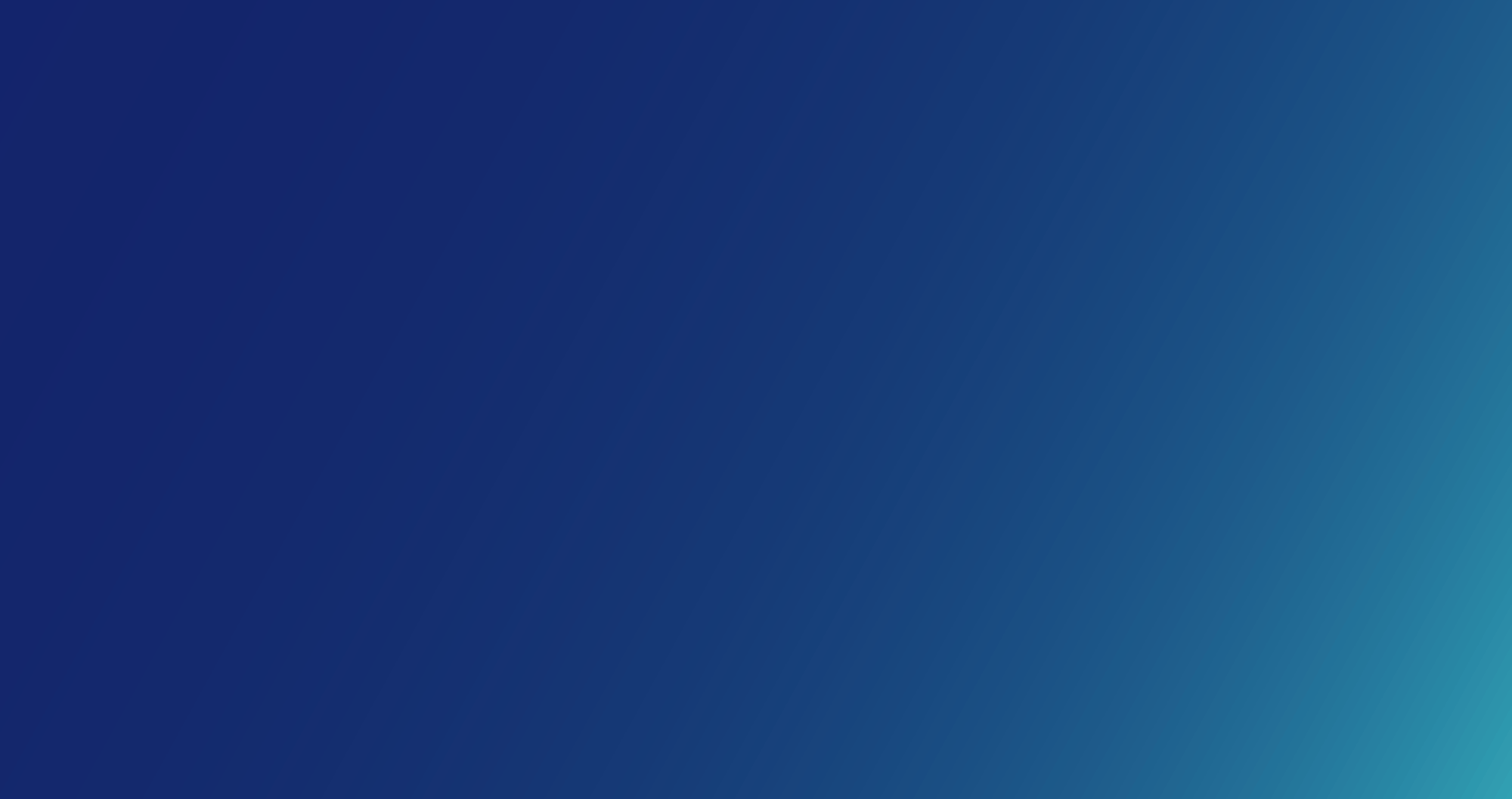
THE PROBLEM
Ammonia has the highest energy density for a zero carbon fuel, however it is not a ‘green’ chemical – Currently it has a significant carbon footprint due to the fossil fuel source of the energy and hydrogen required to make ammonia.
The ammonia landscape has been built on fossil fuel utilisation for the past 100 years. But the climate crisis is dictating a need for change to remove carbon emissions. Fortunately, the ammonia sector can remove fossil fuels through the adoption of renewable electricity and green hydrogen. This provides a carbon zero set of building blocks to produce ammonia. However, the intermittency of renewable energy and the difficulties associated with the handling and storage of hydrogen at an industrial scale present new challenges to the ammonia sector.
Green ammonia production has to be adopted at 3x the current scale in the next 30 years to help address the decarbonisation targets.
Built at scale (small to large)
Lower cost (CapEx and OpEx)
Agile operation
Increased renewable energy utilisation efficiency
Minimize hydrogen storage and buffering
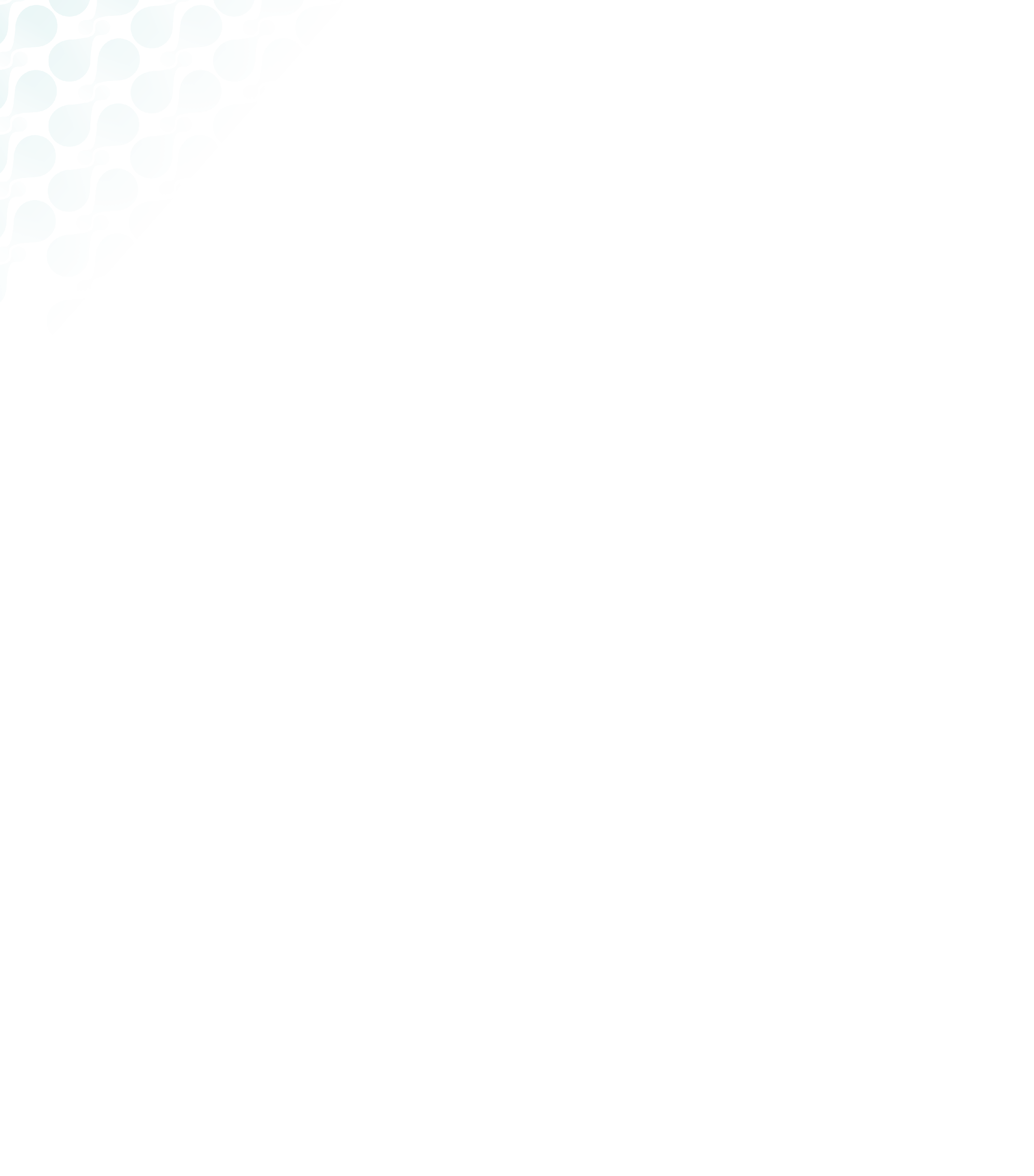
OUR SOLUTION
Liquium’s solution to the upcoming ammonia revolution is at the heart of the process - the catalyst.
Our novel catalysts have industrially relevant chemical and physical properties, scalable manufacturing and world-class low activation energies - aligning to a milder ammonia production process. In addition, Liquium’s ammonia reaction follows the same proven chemical engineering design for a thermochemical reaction, i.e. the Haber-Bosch process (just under milder conditions). This eliminates a major proportion of engineering risk and development for scaling this process to industrially relevant operations.
WHAT’S NEXT
-
Liquium currently has three generations of catalysts for milder ammonia production and new research is underway focused on the next generation. This work is critical to continuously improve the material’s catalytic activity, efficiency and real-world suitability.
-
Liquium’s catalysts are easy to fabricate, store and handle. The team has identified a fabrication methodology to generate sufficient catalysts for the pilot operations. All this work will be completed internally whilst building partnerships with third parties to scope large-scale fabrication for demonstration and commercial facilities.
-
Industrial pilot testing is a critical stage in developing any large-scale manufacturing and processing technology. The team have completed a preliminary design for the industrial pilot facility and is excited to transition from a materials company to an ammonia production company.
-
The team is acutely aware of the toxic nature of handling and producing ammonia. Therefore, Liquium will adapt and adopt the well-established best industry practices for the next stage of the company’s development as it transitions to an ammonia production outfit. The team has established a positive workplace health and safety culture and reporting framework to ensure this is fundamental to all operations as the company grows.
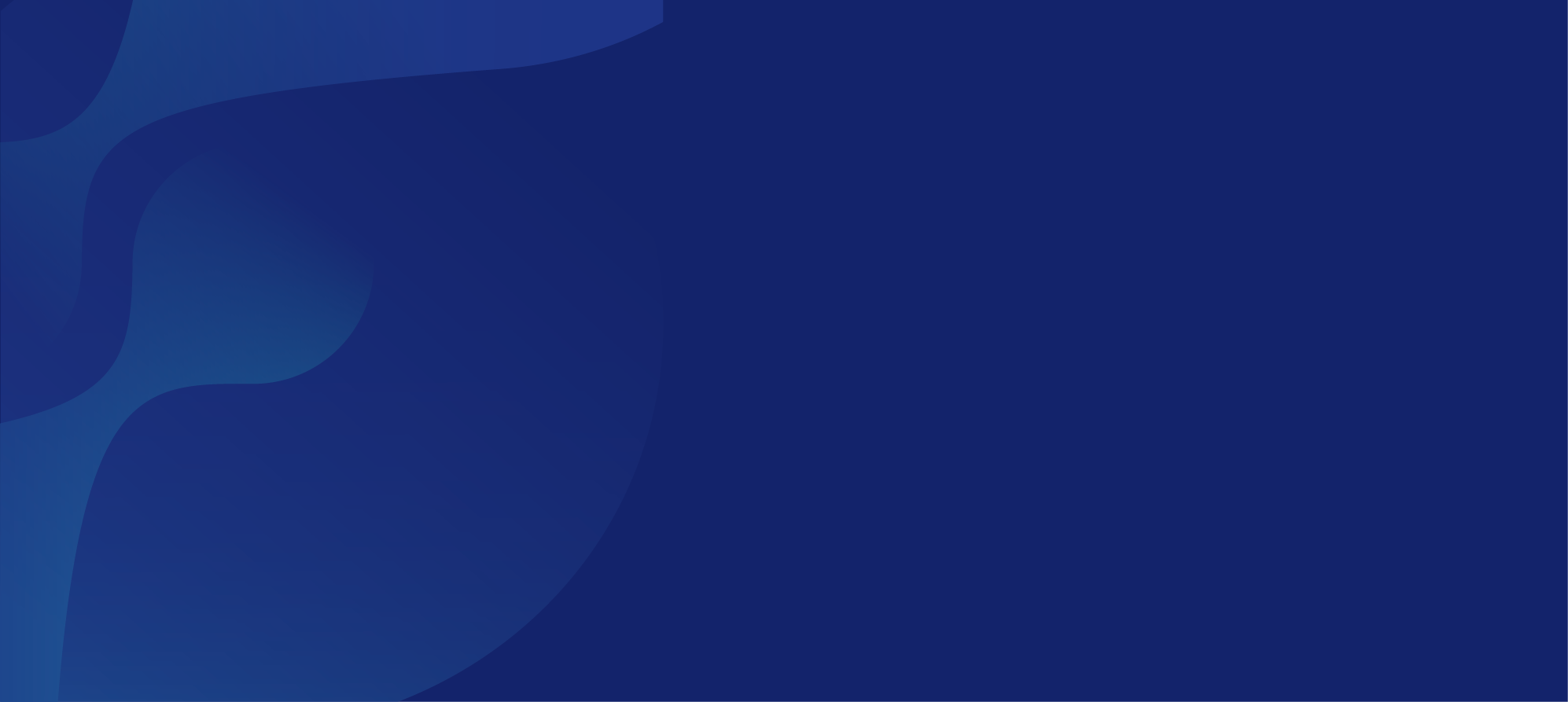
LIQUIUM’S VALUE TO THE AMMONIA PRODUCTION PROCESS
Reduce the cost of Haber-Bosch
Lowering the green premium of new clean fuels is essential. Liquium’s new catalysts enable significantly milder operating conditions for a Haber-Bosch process and thus lower the expensive infrastructure and operation costs.
Align to Renewable Energy
Milder ammonia reaction conditions support a more agile process where faster ramp up/down times are possible and a more efficient utilisation rate of power, less overbuild requirements and hydrogen infrastructure costs.
Scalable technology
Our catalysts are highly active, solid phase, with simple processing to support large scale manufacturing. Secondly, our ammonia reaction follows the proven Haber-Bosch engineering design, signficantly de-risking the engineering development.
Liquium’s technology supports a re-imagined ammonia model where it is applicable for existing and new industrial deployments but also could enable a smaller, decentralised plant
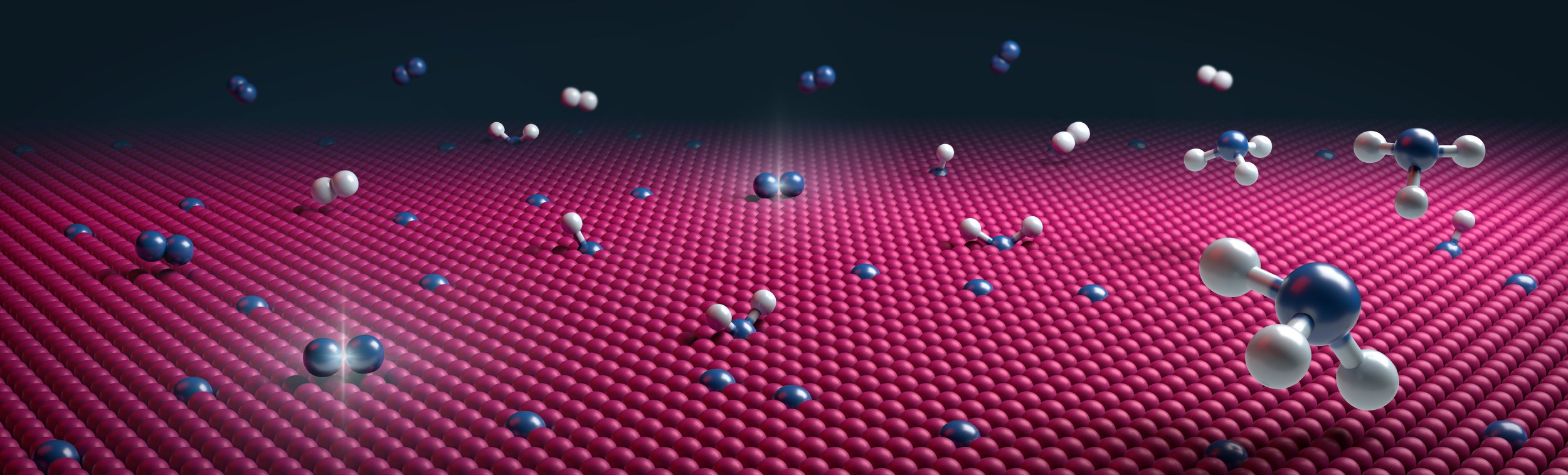